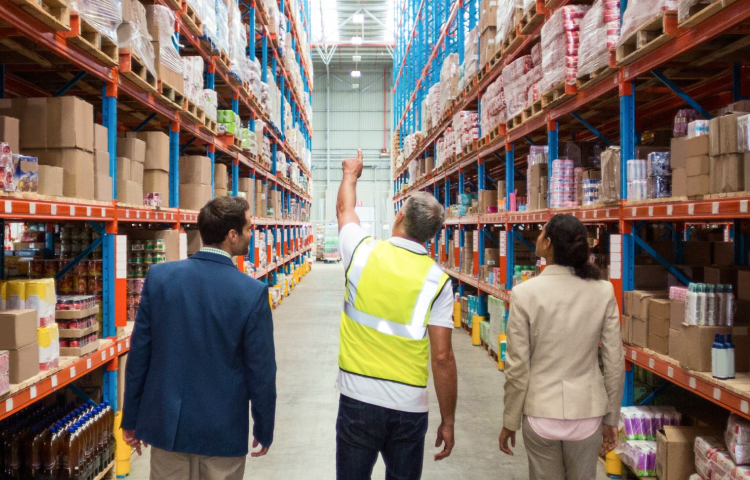
Whether you have a few pieces of assets or thousands, keeping them working at peak performance is vital to your organization. Maintenance is defined as efforts taken to keep the condition and performance of an asset in optimal operating conditions. Evaluation of the condition of the equipment is performed to determine if the asset or a component need to be repaired or changed. Below are the common types of maintenance strategies.
Reactive/Corrective Maintenance
Reactive maintenance also known as “run till it fails” is the process of responding or reacting to equipment as soon as they break down or a malfunction is detected. The aim is to make the equipment function normally again. No actions such as routine inspections or replacement of parts are taken to maintain the equipment to ensure its useful life is reached.
Preventive Maintenance
Preventive maintenance is a type of proactive maintenance that involves taking precautionary actions to prevent equipment failures before they occur. Its aim is to mitigate or detect degradation of a component or piece of equipment to sustain and extend its useful life through controlling degradation to an acceptable level.
In order for technicians to implement such maintenance, they must take the equipment’s history and past failures into consideration to identify the period during which a piece of equipment might break down.
This usually involves routine inspections, upgrades, adjustments and replacement of outdated equipment or components.
Condition-based Maintenance
Condition-based maintenance aims to prevent failures by embedding sensors in equipment that indicate if there is a malfunction or upcoming failure. Technicians monitor key parameters and indicators of the equipment such as temperature, vibrations, moisture and more. This maintenance type monitors the real time parameters and condition of the asset to determine the kind of maintenance required.
Condition-based maintenance allows for last-minute response to a system.
Predictive Maintenance
Predictive maintenance is a type of condition-based maintenance that tracks and measures the performance of an equipment to detect defects and predict its failure. Analysis is done with historical data collected overtime and real time data with more data making predictions better. Predictive maintenance differs from condition-based maintenance in the way that it uses more advanced algorithm and statistical methods such as machine learning or reinforced learning which allows more sensors to be monitored and evaluated.
Smart sensors collect real-time data that determines if there are any abnormalities outside of the normal operating parameters and predicts when and if a failure might occur. Technicians then schedule repairs or maintenance to prevent imminent failures.
Predictive maintenance is considered the most advanced and intensive type of maintenance.
What comes next?
The next step in maintenance management would be to not only have a more technologically advanced but also a more integrated solution. With the need to monitor more parameters, more sensors would be implemented producing more data. The system should be able to monitor the entire process chain offering automated information such as time taken by an operator to complete a task, stock levels in the warehouse and so on.
Implementation of such systems will also bring new challenges of change management and training of resources.
Though in its infancy, prescriptive maintenance is believed to offer endless opportunities. Many experts are considering its potential to be the next step in improving reliability and maintenance.
Prescriptive maintenance also known as RxM takes predictive maintenance one step further. It not only predicts the equipment’s impending failure but also suggests reasons for failure and specialized recommendations to mitigate it.
Prescriptive maintenance is driven by prescriptive analytics. The algorithm analyzes historical data and patterns to provide hypothetical outcomes simulating real life scenarios in order to improve the equipment.
The technological advancements are impacting our day-to-day activities including maintenance processes. An integrated maintenance solution would provide the complete picture of any maintenance task. For instance, having a system which indicates there is a need for maintenance of a machine due in 1 week is only shoing half picture if it doesn’t inform the operators that the part that needs replacement in the machine has a lead time of 4 weeks. In such case the maintenance task though triggered 1 week in advance is still going to create 3 weeks of idle or lost time. The future maintenance solutions having an integrated maintenance system would be covering the entire supply chain providing an opportunity to identify outcomes months before it becomes evident to operators and thus help transform maintenance processes and asset performance.
Get in touch with us today to explore opportunities of digitalization.
If you are interested in exploring digital solutions out there in the market, Dintegra offers a holistic EAM solution for various industries including fleet, facilities, manufacturing and more.